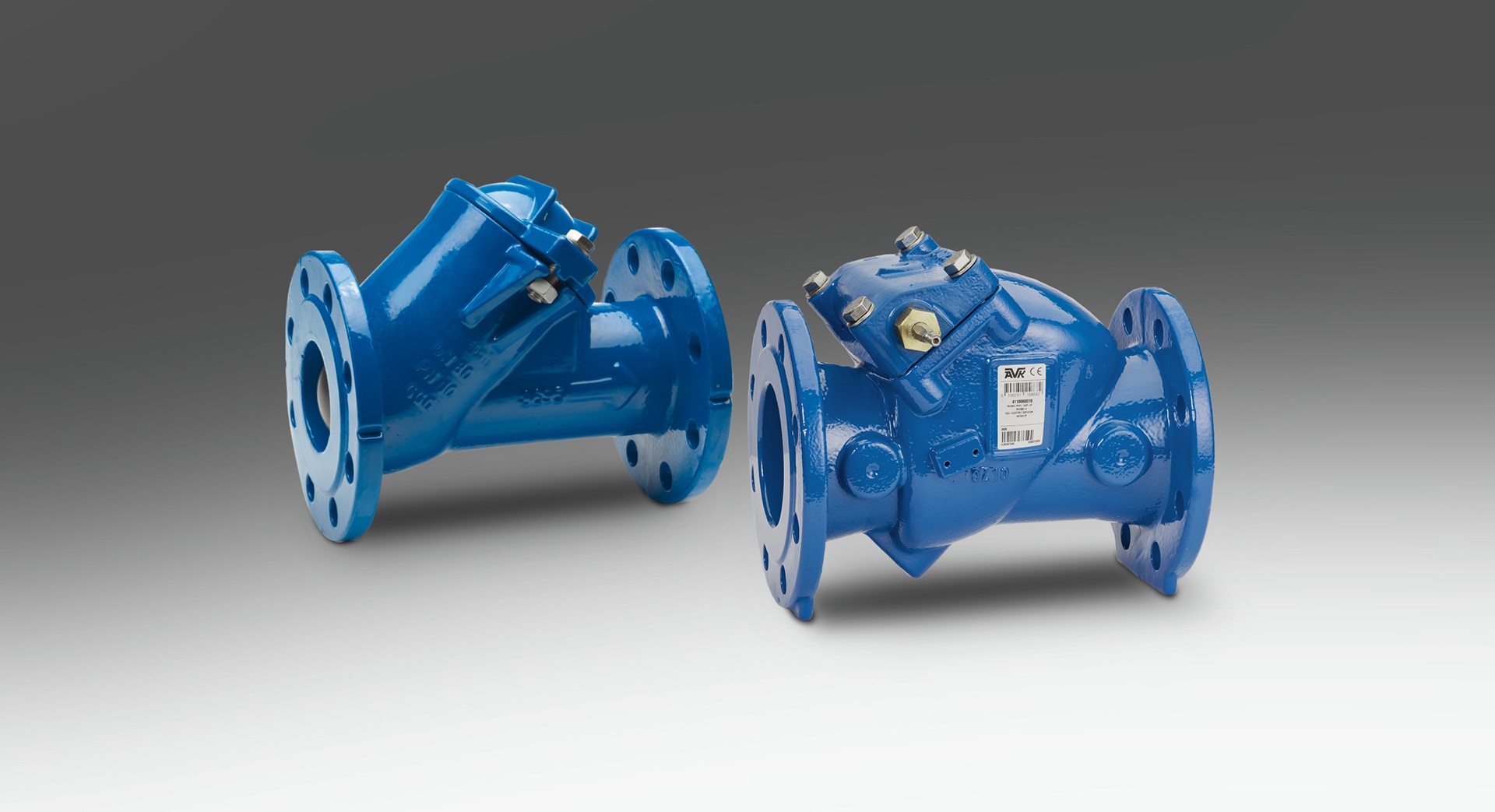
Check valves for water supply and wastewater treatment
What is a check valve?
Check valves are one-way valves installed in pipeline systems to prevent backflow. They allow fluid to flow freely in only one direction and are used for various purposes – for example, to prevent contamination of drinking water, to protect pumps, pipes and other components from water hammer and pressure surges, and to avoid unintended air intake or vacuum in the pipe network.
Where are check valves used?
Check valves are used in many different applications. For instance, they are often placed on the outlet side of pumps to safeguard against backflow. Centrifugal pumps, which are commonly used in water supply systems, are not self-priming, so check valves are essential for keeping water in the pipelines.
Additionally, check valves are widely used in HVAC systems (Heating, Ventilating and Air Conditioning). HVAC systems are for example used in large buildings, where coolants are pumped across multiple floors. In these systems, check valves are installed to ensure that the coolant flows in the intended direction and does not flow back down, maintaining system efficiency and preventing damage.
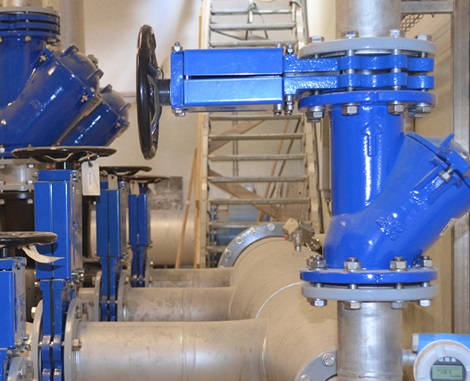
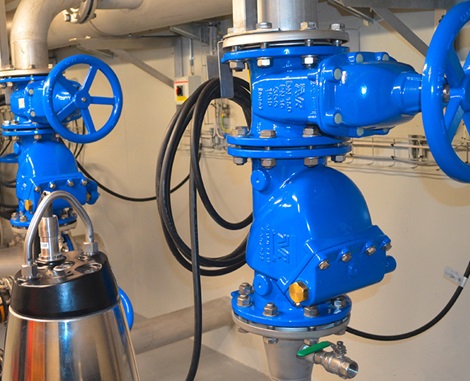
Considerations when choosing a check valve
Choosing the right check valve requires a thorough evaluation of system needs and a cost-benefit analysis. The goal is to balance cost efficiency with minimal pressure loss, but when it comes to check valves, achieving higher safety often entails a tradeoff in terms of pressure loss. To ensure the system is adequately protected, each system needs individual assessment of factors such as the risk of water hammer, acceptable pressure loss, and financial implications of an over-engineered safety margin. For further guidance, refer to our guide on How to choose the right check valve.
Types of check valves
There are various types of check valves available for water and wastewater applications. While they operate in different ways, they all serve the same purpose of preventing backflow. We offer a wide range of check valves, including swing check valves, ball check valves, nozzle check valves and silent check valves. Among the most used types for water and wastewater applications are:
Swing check valves: A swing check valve is mounted with a disc that swings on a hinge or shaft. The disc swings off the seat to allow forward flow and when the flow stops, the disc swings back onto the seat to block reverse flow. Shut-off characteristics depend on the weight of the disc and the return flow.
Ball check valves: A ball check valve functions by means of a ball that moves up and down inside the valve chamber. The seat is machined to fit the ball, and the conical chamber guides the ball into the seat to seal and prevent reverse flow.
Explore our full range of check valves in the product finder.
Water hammer and pressure surges
What is water hammer?
Water hammer occurs when the velocity of a fluid in a pipeline system changes rapidly, typically due to the sudden stoppage of flow caused by an obstacle. This can happen, for example, if a valve is closed too rapidly. A rapid change in velocity will send a shock wave through the pipeline, potentially damaging both pipes and equipment. It will continue to travel along the pipeline until the energy has dissipated, and it can cause a localized increase in pressure and produce loud hammering noises. This is the sound of the pipeline expanding under pressure surges.
Why pressure surges occur in pipelines
Pressure surges arise when a pump stops or a valve closes too rapidly, causing the flow to continue and creating a vacuum downstream to a pump or valve while building up a very high pressure at the opposite end of the pipeline. When different pressures are present in the pipeline, the flow will move towards the low-pressure area, generating a surge that will continue to travel back and forth until the energy has dissipated and the pressure is stabilised.
Although a pressure surge may only be brief, it can amplify system pressure by 10 fold or more, leading to severe damage such as pipe cracks, bursts, cavitation or implosion caused by vacuum pressures. Beyond repair costs and operational downtime, such incidents pose significant health and safety risks. Additionally, repeated smaller surges over time can result in system fatigue failure.